Technical Article
Published 01/2022
Why Specifying Enclosed Epoxy Insulation Delivers Better Reliability
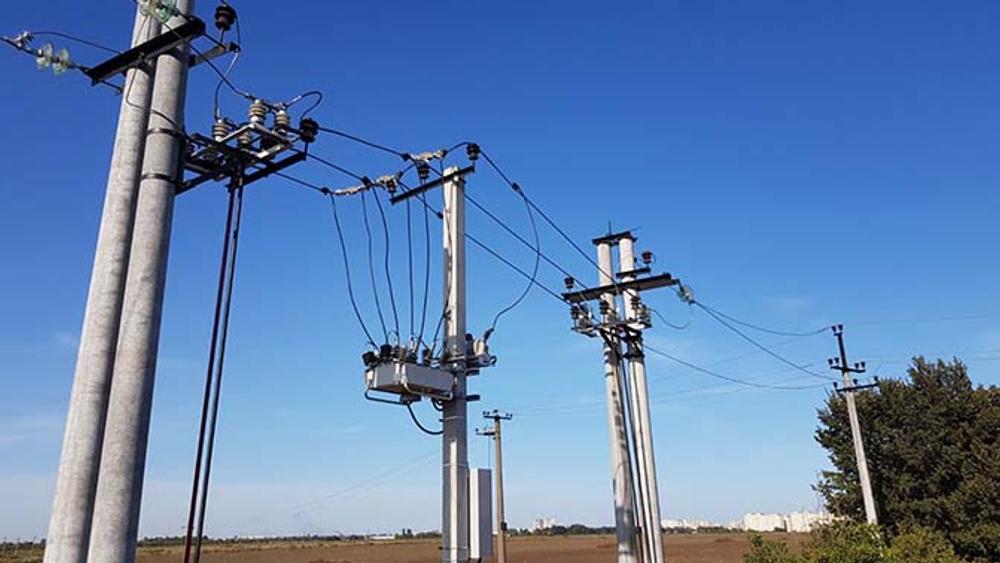
As power systems engineers, our goal is to safely and sustainably deliver reliable electricity to our customers. In years past, our engineering predecessors would specify the latest SF6 gas insulated switchgear to achieve most of that goal. Despite SF6’s environmental damage, they would be forgiven in the context, as they had no alternative when choosing cost-effective switchgear.
Today however, SF6 insulation has been obsoleted by electrical grade solid dielectric. This insulation is an advanced polymer that replaces the role of SF6 in making switchgear. Engineers can now specify solid dielectric as an insulation medium, but this there is a risk in specifying it alone.
The key risk is environmental factors.
Original epoxy insulation provides excellent insulation properties, but resistance to the environment, particularly water, has been subject to extensive research. The engineering problem is that over time, epoxy’s hydrophobicity (its water-repelling ability), degrades. This degradation accelerates in high UV, high rain, or high pollution.
While many materials scientists are working to address this shortcoming, the fundamental weakness of solid dielectric insulation is environmental exposure risk.
What Goes Wrong
Understanding the risk of exposed epoxy in switchgear is best understood with a diagram model. Figure 1 shows this process.
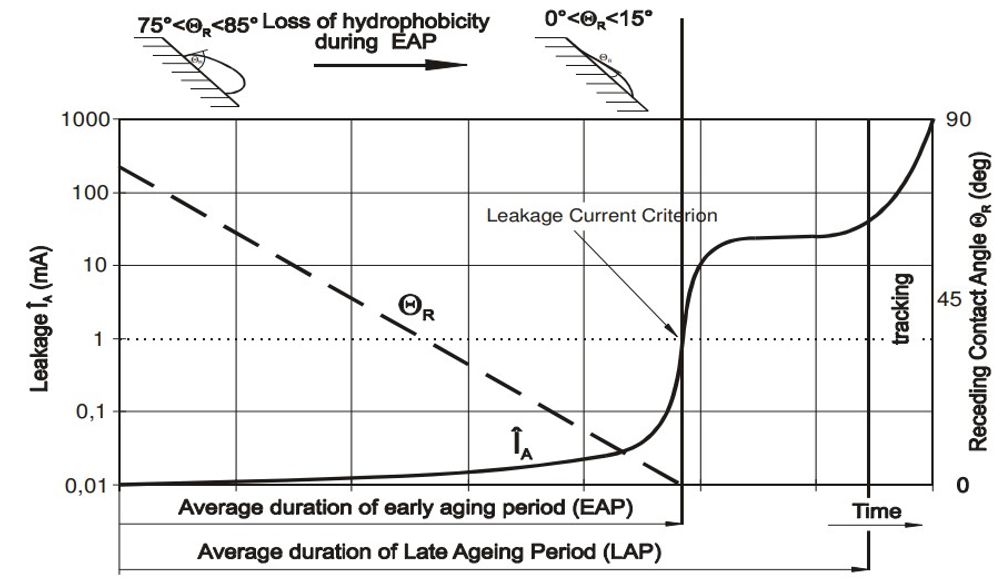
When solid dielectric epoxy is fresh, water forms clear droplets, rather than a film. Over time, environmental factors cause a reduction in this performance. Once a film of water can form on the material, breakdown accelerates. Eventually, electrical tracking occurs, before final arc faults and insulation failure.
Epoxy can be treated with additives, which work to restore the surface integrity, but these too are a finite resource. Once they are exhausted, the film reforms, and the breakdown ensues.
How to avoid it
The best way is to play to the strengths of epoxy, and to keep it away from sun and rain.
By enclosing the epoxy in stainless steel and silicon, engineers mitigate the risk of accelerated environmental aging of equipment.
Across the 104 countries of engineers and 85,000 installations of the NOJA Power’s OSM Recloser, not a single report has been made of environmental-caused insulator failure.
Specifying solid dielectric insulation enclosed in silicone and stainless steel is a solid choice for choosing reliability in power and switchgear products.
“Historically the argument has always been please don't ban SF6 gas use in medium voltage switchgear because we can't make safe reliable switchgear without it,” says NOJA Power Group Managing Director Neil O’Sullivan.
“The reality is using epoxy resin as the insulation system instead of SF6 gas has been used for four decades successfully and reliably. Combine that with an arc fault contained and vented stainless steel tank and you can make safe, reliable, solid dielectric switchgear and completely eliminate the use of SF6 gas for medium voltage applications. It's time we do that globally. Particularly in the race to net carbon zero by 2050.”
Want to stay up to date with Electrical Distribution Technology?
Join our list for a free weekly technical bulletin, as we share our Global Electrical Engineering experience directly to your inbox.
Subscribe →